SACMA founded in 1939, began to design and manufacture cold forging machines just before the world war. The increasing development and substantial growth have brought the name of SACMA to become well known by the world manufacturers of fasteners and special parts. Every day more than 6500 SACMA machines are operating throughout the world, in hundreds of factories, transforming thousands of tons of material into high quality fasteners and special parts, used in many different industrial applications.
For the industry that mass produces consumable items, like fasteners, the advantage of cold forging is an inevitable consequence for reasons of high strength, tight tolerances, reduction of waste material, low energy consumption rates, competitiveness and productivity.
Within the strategy of supplying machines with the highest technology levels, SACMA continues to improve and develop new model progressive cold formers and combined bolt makers, supplying them to the ever growing market of net-shape parts with state-of-the art technical contents.
End users have a high appreciation of SACMA machines, considering them to be well designed, well manufactured, powerful, adaptable for making special parts, flexible for making long or short parts, fast and reliable whilst providing low cost production.
In order to assist all its Customers around the world, SACMA, has developed worldwide efficient service centers able to supply any spare part in a very short time to keep Customer machines running and making parts.
In the next pages we would like to give you a clear picture of what are the Winning Technologies® that have made SACMA so famous and successful in the world.
MONOBLOCK MAIN FRAME
The main frame is a fundamental element for performance of any machine, particularly of a cold forming machine, because it imparts rigidity, precision and reliability in time.
For this basic component the experience gathered over the years, the research with the most sophisticated simulation methods and the experimental analysis of deformation have been prime elements of design.
Among the different methods of manufacture Sacma has chosen the monoblock casting made of perlitic spheroidal cast iron, normalized and stabilized by ageing in excess of 12 months, to guarantee the maximum rigidity and the highest level of stability under heavy loads.
Furthermore, the selection of the best suppliers of castings together with a constant monitoring of conformity to the Sacma technical specifications are the best guarantee of constant quality.
The accurate machining, the strictness in process controls, the high degree of suppression of vibrations, a typical characteristic of this material, make our machines perfectly capable to produce parts with constant standards of precision, for many years.
ULTRA PRECISION
The high degree of precision in machining is a must for manufacturing machines that must operate with high productivity and efficiency.
In order to reach this objective, there must be no compromise of quality of any mechanical component present in machines that undergo high stresses such as cold formers.
Sacma has chosen to manufacture, in house, all components and has installed the most modern production machines available today on the market, to promote the total quality of all its products.
A systematic and rigorous inspection procedure of all manufactured parts before inventory stocking is the best guarantee of interchange ability and availability of spares.
The correct choice of high tensile materials, the proper heat treatment specifications, the accuracy of surface finish operations of grinding and lapping make a Sacma machine the most reliable, the most productive and lowest cost machine in manufacturing.
QUICK CHANGE AND QTC PACKAGE
The concept of performing tool change in the shortest possible time represents an undisputed necessity for modern industrial manufacturing of cold forged parts, made in smaller lots, making forming more competitive against traditional machining methods.
In developing the tool change system, Sacma made no compromises of rigidity and power of the machines; a typical characteristic of its machines.
The CR quick tool change system, standard for machines series 3, 4, 5 and 6, allows for easy removal of the die block, hydraulic clamped, and just as easy removal of the punch block bolster and the complete transfer unit.
For a real quick change of the tool holders some options can be added : an operator set up bench for punches and dies, a service trolley, a complete external tool alignment and set up bench and a jig for transfer finger centering outboard of the machine the optional QTC package includes a punch holder plate, a die box, an extra transfer beam with trolleys and a jig for the transfer finger centering which enables an easy and quick tool change, to be done by using the supplied flag crane or the optional gantry crane.
TOOL PRESETTING
The Sacma - CR Quick Tool Change machines, designed to perform production changes in a short time, still maintain the renowned characteristics of robustness, precision, reliability and efficiency, typical of a SACMA machine.
The Sacma machines can be equipped with an external Presetting Bench for setting the tools.
The pre-setting bench helps making a precise centering among dies and punches, their accurate setting by using the wedges integrted in the removeble punch holder plate itself. This procedure is best performed in the tool room area, or next to the machine by the operator ensuring that the tools are ready to be set-up in the machine. This allows a more rational utilization of the factory floor space and the optimization of the company’s technical resources.
LOAD MONITOR SYSTEMS
In order to produce constant quality, monitoring systems are today a must on all multi station cold forging machines.
Monitoring of cut off lengths and of forging and roll forming loads, over and above the safe guarding of the tools and of mechanical organs of machines, is also an effective indirect control that parts are produced to print.
All Sacma machines are fitted with state of the art control and monitoring systems, developed in conjunction with a leading manufacturer in this field. SC10: Short feed control system, supplide as standard equipment on all CRM progressive and combined headers;detects the blank with a shorter length than the setted one and discards it, opening the first transfer finger automatically. It is also possibile to set the max. number of subsequent scraps, before stopping the header.
SC500: Forging load monitoring system, calibrated to give a true reading of the total load and of the two components in the main frame of the machines.
It is supplied as standard on every progressive and combined header, very useful to protect the header against overloads and to check the right setting of the tooling. Thanks to two piezoelectric sensors on the shoulder of the header, the heading load is measured in k-Newton. The device displays the total load on the control panel and the components on each shoulder, at every slide hub. The protection against overloads stops the header immediately as soon as the setted parameters are overcome. Every machine can be prepared for the installation of other load monitoring systems according to the Customer’s needs or equipped with the Sacma Loadmatic unit for the load monitoring in the single stations. On the combined headers a thread-rolling load monitor system SC600 is available: thanks to the optimized sensorization of the fixed tool holder block, it can detect the smallest threading flaws and discard the n.c. parts automatically by means of the pneumatic door.
HYDRAULIC CLAMPING
Hydraulic clamping of adjustments and tools is of great help when setting the machine and guarantees repeatability of the adjustments.
Clamping and unclamping is easily performed by the touch of a switch, avoiding any manual work with wrenches inside the machine enclosure.
All Sacma machines are fitted standard with hydraulic clamping of die side adjustments of threaded sleeves, kick out levers and trim cam in the last station.
All CR quick tool change machines are supplied with hydraulic clamping of the complete die box.
On the Series 6 machines the complete transfer finger unit and the timing cam shaft are secured in place by hydraulic clamping.
The new SP 670, large 6 die cold former, has hydraulic unclamping of the individual finger timing cams which can be adjusted automatically.
HIGH PERFORMANCE SLIDE
The main heading slide is the element that delivers the energy of deformation and as such it must have great stability and robustness. Furthermore the heading slide must run perfectly true to the dies at every stroke, with high precision.
All Sacma machines heading slides are made of NiCrMo alloy steel casting, heat treated and having a special geometric shape with double slide ways to offer maximum stability in delivering the forging energy to the tools.
An efficient lubrication system makes sure that slide ways are always well lubricated even under the worst and unbalanced forging conditions.
An exclusive taper slide way guarantees a perfect alignment of the tools at every stroke, permitting therefore production of all parts that require extreme tolerances.
TRANSFER SYSTEM
The real heart of high speed horizontal cold formers is represented by the transfer mechanism which has to be able to bring parts from one station to the other: only with a precise and infallible grip can one obtain best results of efficiency and productivity.
The transfer mechanism of Sacma Progressive and Combined headers is by far considered the world benchmark, so much, that it has been subject of numerous unsuccessful imitation attempts by others.
The precise movement of the transfer fingers, determined by a smooth oscillating mechanism generated by perfect Desmo drive double cams imparts to the whole system a perfect control of position also at the maximum production speeds.
At the discretion of the user, the last two transfer fingers are available to be opened pneumatically and with interface with the load monitor system for a perfect quality management. Alternatively the pneumatic opening can be extended to every transfer finger to automate the emptying operation of the fingers. The transfer can be equipped with the SC800 device, to detect the blank in every single station of transfer. It leads to the immediate stop of the header in case of part’s loss.
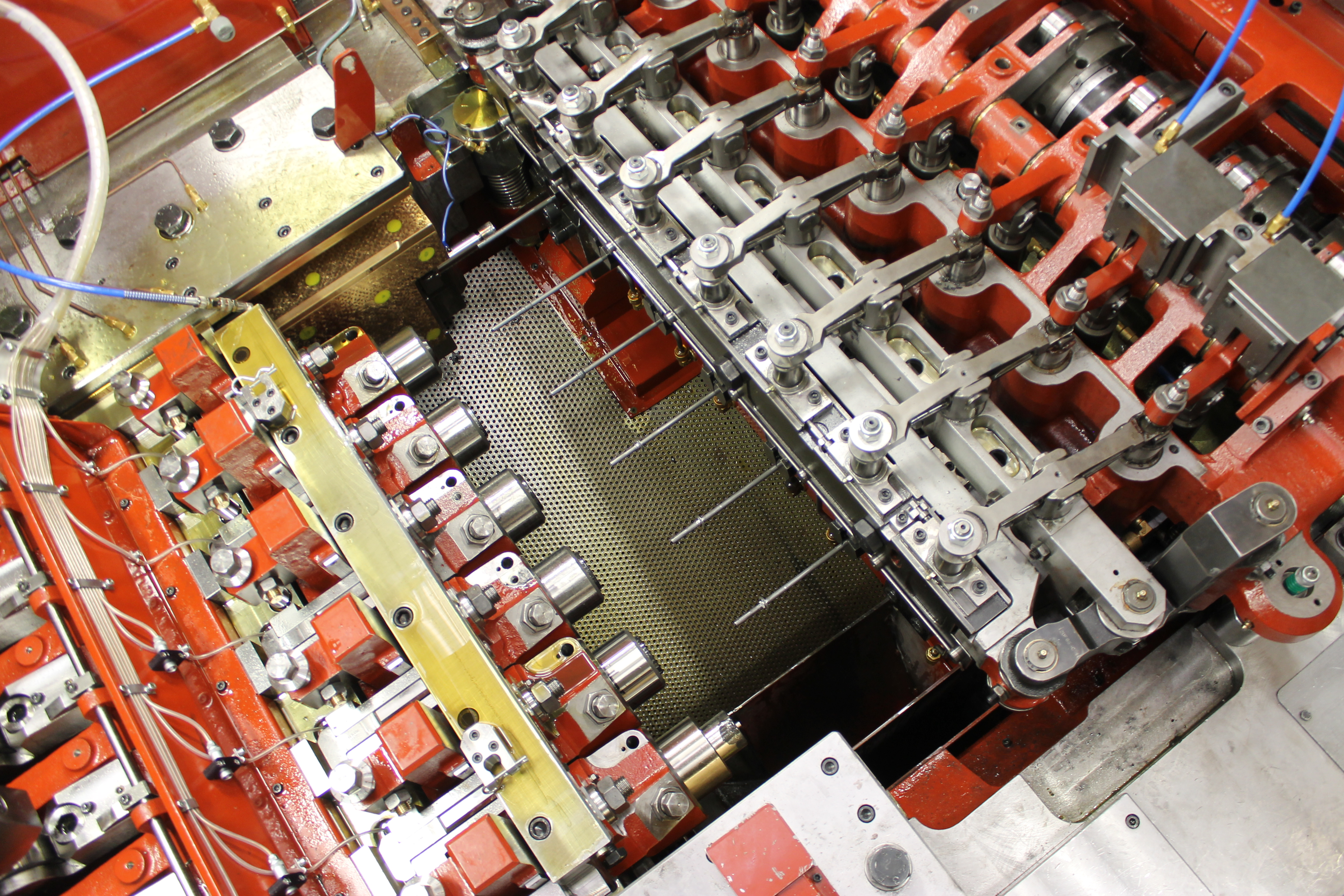
S-TRANSFER (PATENTED)
On 6-die headers size 4, 5 and 6 the new S-Transfer is available as optional equipment. It combines all the traditional characteristics with the flexibility and user friendliness, typical of the meccatronic apps.
The registrable camshaft is replaced by some electrical linear operators which activate the transfer fingers. Through the control panel, with an efficient and intuitive interface, the operator can set both opening/closing times and speed of every pair of fingers, together with tightening force and timing of the transfer cross motion.
The setting data of every product code are stored in the machine PLC and recalled when needed.
The advantages of the S-Transfer are very clear:
-decrease of the change over time
-first setting very simple and user-friendly
-chance to select three finger opening/closing speeds: normal, fast and ultra-fast
-monitoring of the blank’s presence in the fingers
-chance to open the fingers independently, by means of manual command or signal of the load monitor system
-closing force of the single fingers which can be selected by the operator panel.
The operating safety is granted by the fly-wheel regenerative activation, which avoids damages coming from the sudden lack of power supply.
The solidity and the lifespan are backed up by a refrigerating group keeping the linear motors in an optimum temperature range.
TRANSFER SUPPORT ASSIST PACKAGE
A good and efficient transfer system must be able to transfer from one station to the next any type of part, independent of geometry and length.
For this reason a special transfer assist system has been developed to operate in perfect timing with die kick-out, to transfer with ease all those difficult parts. The well known and great capability of the SACMA transfer to handle difficult and short parts, now becomes all the more versatile with the introduction of a patented SACMA transfer support assist package, that can transfer conical or shoulder parts which would tend to fall in the ejection phase. The system consists of support fingers, perfectly timed with the motion of the transfer and of the kick-out rods, brought about by a direct link with the rods and a Desmo Drive system of double cams which controls the lateral movement.
This system is now available on headers from size 1 to size 6.
SERVICE EQUIPMENT
Intervention of the operator in the working area must be performed in absolute safety and comfort.
This necessity is particularly felt when working with large machines, in order to facilitate tool change and maintenance procedures.
The patented system of ergonomic platforms and tool cradles supplied by SACMA on the Series 6 machines is a very good example of assistance, without compromise, to the requirements of the end user. The system consists of two hydraulic operated platforms that position themselves automatically over the work area:
- the lower platform used for tool change during production, which can be easly removed by means of a magnetic socket:
- the upper safety platform is used for potential regulation intervention and tooling inspection of the operator when changing or setting transfer fingers and timing cams.
Manipulation of die boxes, punch block bolsters and transfer finger units are performed by means of special cranes that can be fitted on Customer’s request:
- gantry portal crane with electric hoist having three dimensional motorized movements;
-automatic portal with presetting of the holding and positioning tooling operations. Available on headers size 6.
ELECTRONIC HANDWHEEL
Whenever making final adjustments of the transfer it is very useful to have the possibility to verify the correct timing of transfer fingers, to avoid dangerous collisions of the punches with the fingers, even if tools have been designed and manufactured perfectly.
With the intention of assisting best the tool setters in the delicate moment of tool and timing adjustments, Sacma has developed an electronic andwheel to move the whole machine at slow motion in order to check for correct timing of the transfer fingers with respect to the heading slide, avoiding dangerous collisions. The heading slide can be stopped in any position avoiding machine jogging and damaging the main clutch/brake unit.
This special unit is available for all SACMA progressive and combined machines.Moreover the combined headers are equipped with inverter drive also to the pointing spindle motor to optimise cutting speed to the shape of the point and type of material.
COMBINED MACHINES
The proper and best answer to high productivity requirements, rationalization of production methods, floor plan lay-out and material flow in a fastener manufacturing environment is represented by machines that have forging, pointing and thread rolling stations, all in one.
These machines will determine maximum efficiency and quality in the manufacturing process of standard fasteners and special automotive fasteners, because they supply the finished product.
The Sacma Combined headers maintain all the mechanical and performance qualities of the Progressive headers, from which they derive.
The pointing and the thread rolling units are designed and manufactured to be user friendly and easy to set up, to produce many different shapes of points.
When producing very short parts, head heavy parts, or parts that would have difficulty in feeding to the pointer unit using the standard finger elevator, SACMA offers the “V” version of combined headers which use a vibratory feeder to overcome all difficulties.
WARM FORMING
Almost 15 years ago Sacma brought in the branch the first WF progressive headers for the aerospace sector. It was fully integrated with wire warming functions and thermoregulation of the tools and of the cooling oil. In the following years a great developing process took place: nowadays it is therefore for us possible to display the largest and most updated range of WF or half-warm headers’ range, which has been studied to meet every customer’s needs.
According to the material and therefore to the temperatures to be reached, we have the WF300, WF500 and WF900 versions, listed in various sizes.
The WF300 headers size K, 1, 2 and 3 are suitable to the production of bolts and full special parts with normal inox steel and aluminium alloys.
The WF500 headers size 2 and 3 are suitable to the production of hollow parts with the above mentioned materials.
The WF900 headers size 2, 3, 4 and 5 can work to 900°C with the typical materials of the aeronautic industry (inox steel for high temperatures, Nickel superalloys, titanium alloys, steel Ni-Cr-Mo) and on high carbon steel (100Cr6) used in the bearings industry.
Besides the already complete standard equipment, the WF headers can have some optional equipments to make them more performing to the customer’s needs.
Among others, the partial warming system spot heating, the micro-lubrication of the tools, the fire-extinguishing system.
S-TOOLING
The constant evolution of the forging world forces tool design engineers to develop tooling technology to greater levels, in order to produce always more special and difficult parts. Today, in the planning stages of new investments, it is all the more important to be able to rely on the support of a trustworthy partner who has experience in tool design and forming progression, to develop a suitable forging method to manufacture the parts in question.
The long term experience and know-how that Sacma has of analysis of forging problems and in the research of suitable technical solutions, which are then shared with the customer, makes us a valid partner to be of assistance during the critical stages of development, to bring the project to a successful solution in the shortest possible time. A team of project engineers, assisted by modern design and calculation software, works together with the customer to reach the best manufacturing solutions for the industrial development of the product.
The S-Tooling activity involves some steps which include the definition of the optimum deformation sequence by means of the refined fem simulation software, the 3D model of the forming tools, the 2D construction drawings of the single tools, the complete tooling and its test.
With the co-operation of other leading companies in our industry, Sacma is also able to suggest efficient turn key solutions of the projects.
SacmaForm®
Modern fastener manufacturing companies must be able to respond promptly to the production enquiries they receive from all potential customers.
It is therefore necessary to have available a technology that can reduce time for evaluation of the capability and development of the forging process of new parts, to facilitate the choice of the most suitable machine for production.
Sacma, with the cooperation of the Mechanical and Application Engineering Department of Padua University, developed the SacmaForm®; application software, which gives tool designers a valid method and assistance for the initial engineering development of a product.
Starting from a tool progression design and the characteristics of the material, the SacmaForm® software offers a simple and intuitive method for calculation of volumes and forging loads, together with other necessary data for evaluating the economics of the project.
A large and rich library of materials, specific data and examples, useful for tool design, are included in the software.
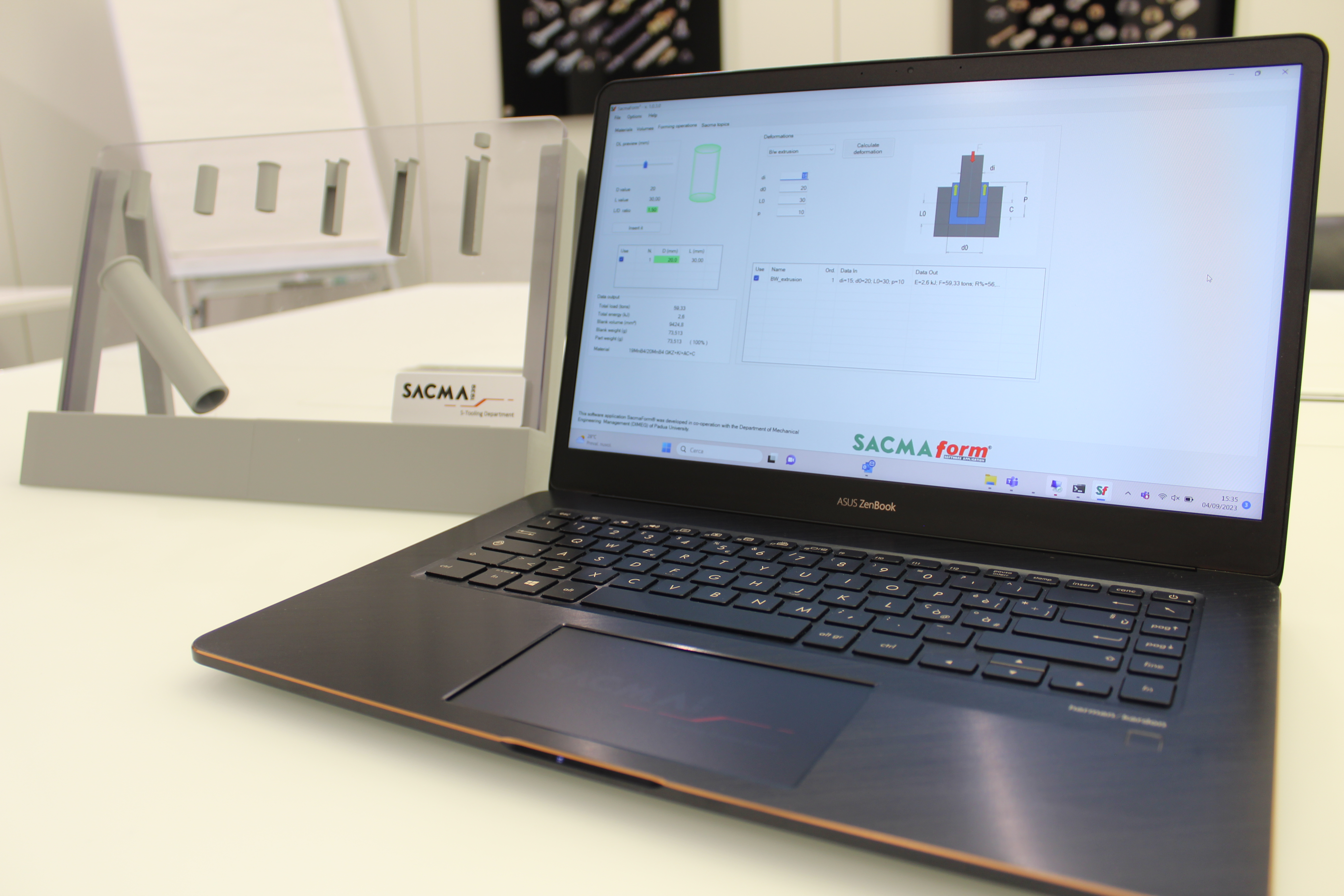
TR THERMOREGOLATION UNIT
he thermoregulation of an header and its tools is not only a cooling procedure, it involves the chance to pre-warm the system to reach the wished temperature range. Therefore the thermoregulation group should be equipped with resistors and chillers. Other essential components are the temperature sensors, the sealed fluid carrier circuit, the heat exchangers and the circulating pumps.
The aim to have an header with a TR system is to improve the precision of the produced parts, avoiding the heating deviation, and during the temporary phases, by reducing the scraps in the production start-up.
It is therefore necessary to thermically stabilize the functioning conditions of the machine, tools and cooling oil.
By setting the temperature on the control panel the TR system can keep it constant, by automatically modulating the warming and cooling phases.
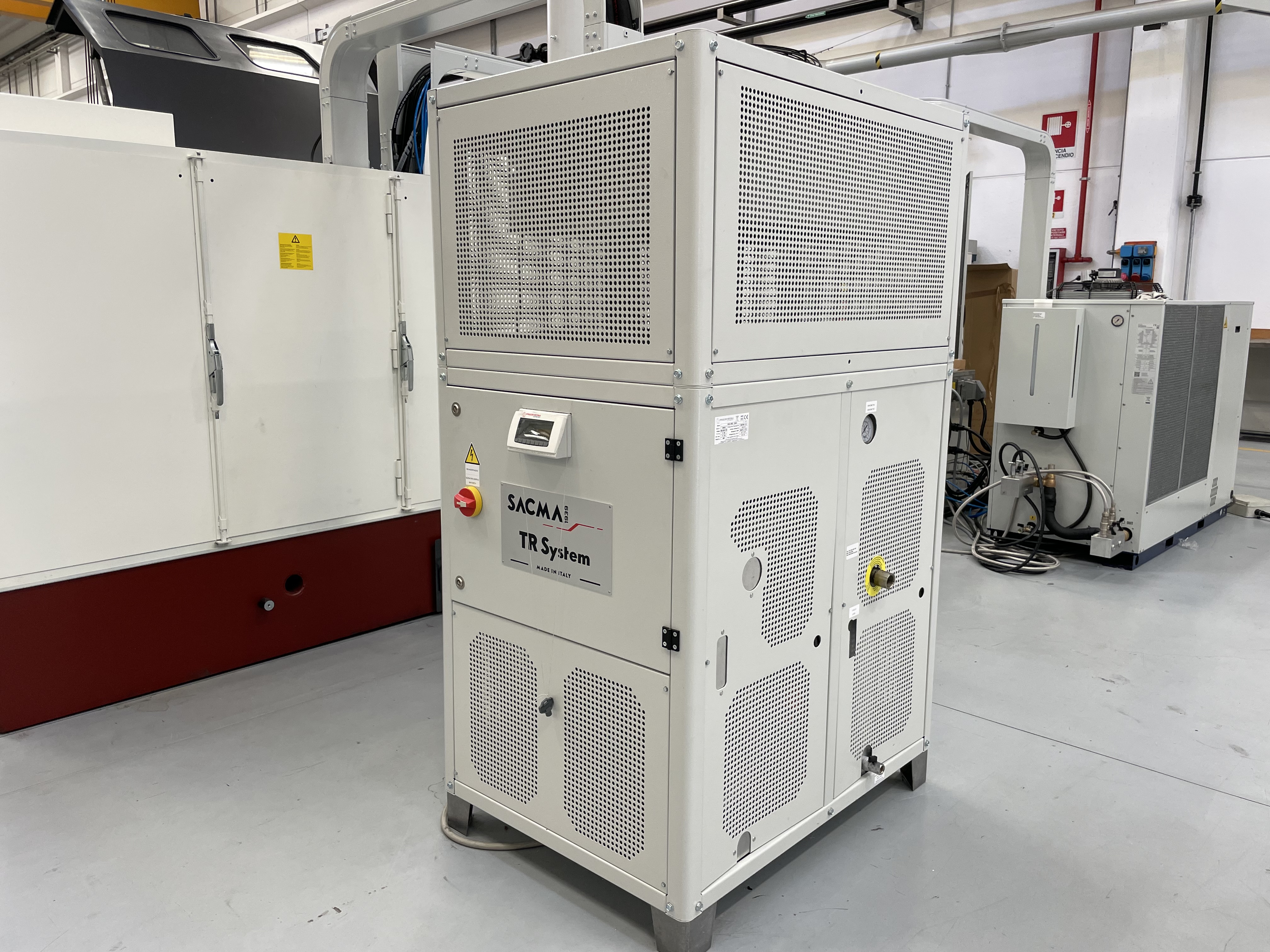
FEEDING AND RE-FEEDING SYSTEM
In the production of especially complex parts it is necessary to deal with the material strength to support high deformation levels. It is typical in these cases to use intermediate annealing treatment to regenerate the material structure.
Hence the need to form in two or more phases: to overcome this need, Sacma developed for its headers some updated and flexible slug or blank feeding systems or re-feeding of pre-formed parts.
These sophisticated processes require a development aimed to the type of parts to be produced by co-operating with the Customer.
The various successful projects of the last decade enable Sacma to set itself as an expert and reliable partner in this activity.
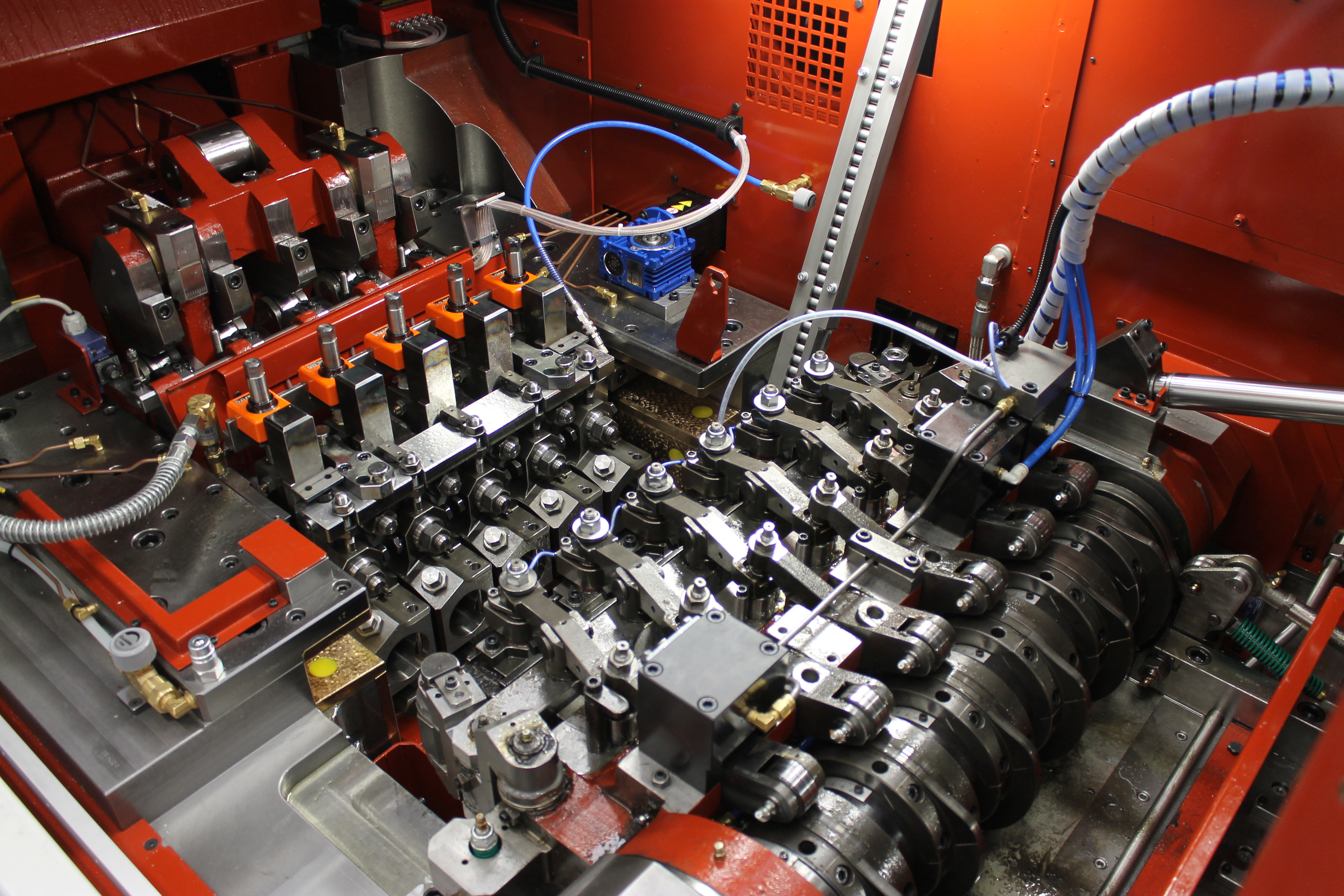
4.0 INDUSTRY
Sacma headers are classified under the category “machines for the plastic deformation of metals and other materials” and distinguished by the following contents, thanks to them they are considered production plant for industry 4.0 with full rights.
Last generation PLC control with integration I/O and MPI or Profinet interface.
Possible connection to the business IT system with TCP-IP protocol by means of LAN or Wi-Fi.
Interface with other machines in the production cycle, which can be managed by the main operator panel.
Interface operator-machine with simple and intuitive icons, with description and diagnostic messages.
Tele-service equipment, remote control and tele-diagnostic, via cable, Wi-Fi or modem USB.
Machine preparation for process supervision systems through heading load monitoring.
Ergonomics requirements, active and passive safety, health and hygiene as per CE legislation.
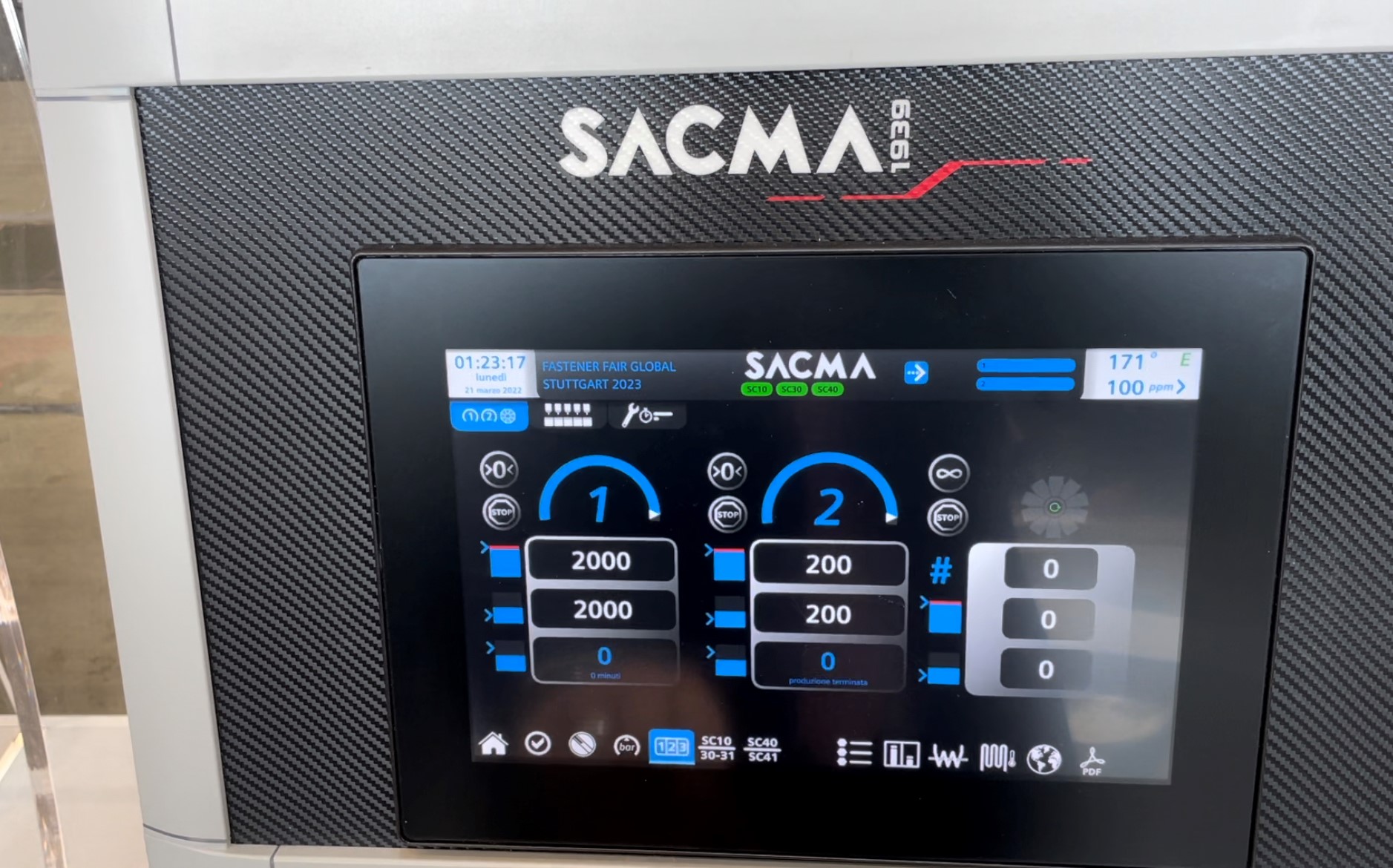
KSP DOUBLE STROKE COMBINATION PRESSES
A soundproof cabin with modern lines and high ergonomics makes the operator's work particularly comfortable.
The sophisticated optional effort control system supervises the press, tools and rolling machine, providing consistent support for product quality and plant protection.